Spis treści
w ilu stopniach topi się plastik?
Plastik topi się w zróżnicowany sposób, a temperatura topnienia zależy od rodzaju tworzywa. Niektóre plastiki stają się elastyczne już przy 100°C, podczas gdy inne wymagają od 120°C do 270°C, by zmienić stan skupienia. Temperatura topnienia plastiku odgrywa kluczową rolę w jego przetwórstwie. Przykładowo, polietylen (PE) topi się w przedziale 120°C – 180°C. To wiedza istotna dla efektywnego i bezpiecznego wykorzystania tego materiału w przemyśle.
Jakie są różnice w temperaturze topnienia różnych rodzajów plastiku?
Różne tworzywa sztuczne charakteryzują się odmiennymi temperaturami topnienia, co jest bezpośrednio związane z ich indywidualną budową chemiczną i specyficzną strukturą cząsteczkową polimerów. Spójrzmy na zakres temperatur topnienia dla kilku popularnych materiałów:
- Polietylen (PE): od 120°C do 180°C,
- Poliwęglan (PC): około 230°C,
- Akrylonitryl-butadien-styren (ABS): około 240°C,
- Poliamid (PA) (nylon): około 255°C.
Należy jednak podkreślić, że dokładne wartości temperatur topnienia są uzależnione od konkretnego gatunku polimeru, a także od zastosowanych dodatków w mieszance, które mogą modyfikować właściwości termiczne tworzywa. Dlatego precyzyjny dobór temperatury podczas procesów obróbki, takich jak formowanie wtryskowe, wytłaczanie czy termoformowanie, ma kluczowe znaczenie dla osiągnięcia wysokiej jakości i trwałości wyprodukowanych wyrobów.
W jakiej temperaturze topnieje polietylen (PE)?
Polietylen (PE) to wszechstronny materiał termoplastyczny, którego temperatura topnienia oscyluje w dość szerokim przedziale – od 120°C do nawet 180°C. Kluczowym czynnikiem wpływającym na ten parametr jest typ polietylenu. Wyróżniamy przede wszystkim dwie główne odmiany:
- polietylen o niskiej gęstości (LDPE),
- polietylen o wysokiej gęstości (HDPE).
LDPE charakteryzuje się niższą temperaturą topnienia, typowo mieszczącą się w przedziale od 110°C do 130°C. Z kolei HDPE, ze względu na swoją strukturę, potrzebuje wyższej temperatury do przejścia w stan płynny, zwykle od 120°C do 180°C. Ta różnica w zachowaniu wynika bezpośrednio z budowy łańcuchów polimerowych, które składają się na te dwa rodzaje tworzywa.
W jakiej temperaturze topnieje polipropylen (PP)?
Polipropylen (PP) przechodzi w stan płynny w temperaturze około 160°C – właśnie wtedy topnieje. Ta konkretna wartość jest niezwykle istotna, zwłaszcza w zaawansowanych metodach obróbki tworzyw sztucznych, takich jak formowanie wtryskowe czy wytłaczanie. Dzięki tej wiedzy możemy precyzyjnie dostosować i zoptymalizować parametry tych procesów.
W jakiej temperaturze topnieje polichlorek winylu (PVC)?
Polichlorek winylu, szerzej znany jako PVC, ulega topnieniu w zakresie temperatur od 180°C do 270°C. Ten stosunkowo szeroki przedział jest wynikiem różnic w składzie chemicznym oraz obecności rozmaitych dodatków. Przykładowo, obecność plastyfikatorów znacząco obniża temperaturę, w której PVC zaczyna wykazywać cechy plastyczne i staje się miękki. Z uwagi na możliwość degradacji materiału i uwalniania szkodliwych substancji w zbyt wysokich temperaturach, obróbka PVC wymaga niezwykłej precyzji i dokładnej kontroli termicznej. Kluczowa jest więc duża ostrożność.
W jakiej temperaturze topnieje poliwęglan (PC)?
Poliwęglan (PC) charakteryzuje się temperaturą topnienia wynoszącą około 230°C, co stanowi kluczową właściwość determinującą jego szerokie zastosowanie. Ze względu na swoją odporność na wysokie temperatury, poliwęglan doskonale sprawdza się w różnorodnych aplikacjach, gdzie ta cecha jest szczególnie ceniona. Temperatura topnienia PC odgrywa istotną rolę w procesach produkcyjnych, takich jak formowanie wtryskowe i wytłaczanie, gdzie precyzyjna kontrola temperatury jest niezbędna do uzyskania trwałych i wysokiej jakości wyrobów.
W jakiej temperaturze topnieje akrylobutylostyren (ABS)?
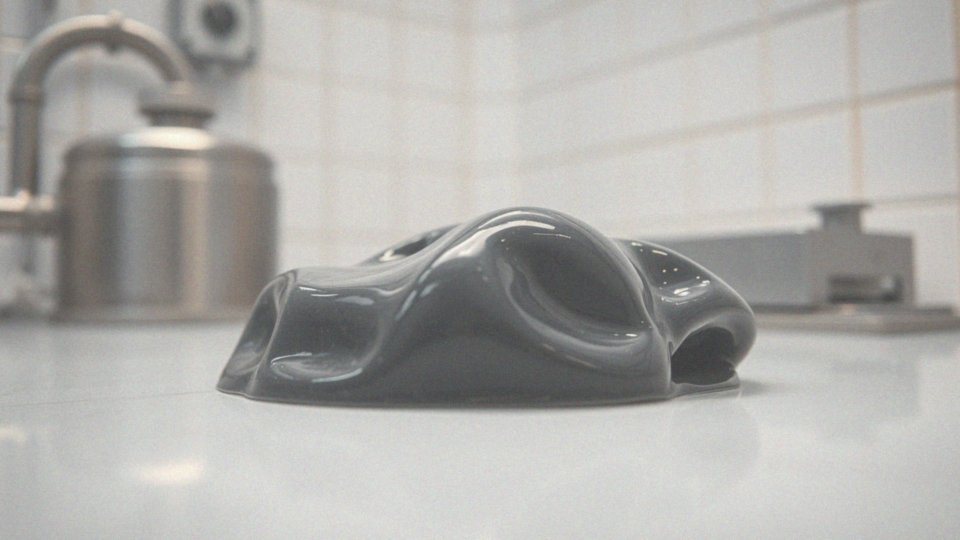
Akrylonitryl-butadien-styren (ABS) to termoplast, który topi się w temperaturze około 240°C. Ta właściwość ma zasadnicze znaczenie, szczególnie podczas jego obróbki, np. w procesie formowania wtryskowego, gdzie precyzyjna kontrola temperatury jest kluczowa. Charakteryzuje się on wysoką odpornością na uderzenia i rozciąganie, a także odpornością chemiczną. Temperatura topnienia bezpośrednio wpływa na jego płynięcie, a co za tym idzie, na zachowanie materiału podczas obróbki, pozwalając na lepszą kontrolę nad całym procesem formowania.
W jakiej temperaturze topnieje poliamid (PA)?
Poliamid (PA), znany powszechnie jako nylon, charakteryzuje się temperaturą topnienia oscylującą wokół 255°C. Warto jednak pamiętać, że dokładna wartość tej temperatury jest zależna od konkretnego typu poliamidu – tak więc, Nylon 6 będzie zachowywał się inaczej niż Nylon 66. Materiały te zyskały uznanie przede wszystkim dzięki swojej wyjątkowej wytrzymałości mechanicznej. Dodatkowo, cechują się wysoką odpornością na ścieranie. Dzięki takiemu połączeniu korzystnych cech z odpornością termiczną, poliamidy są niezastąpione w wielu zastosowaniach, gdzie wymagane są niezawodne i trwałe materiały.
Dlaczego temperatura ma znaczenie w procesie topnienia plastiku?
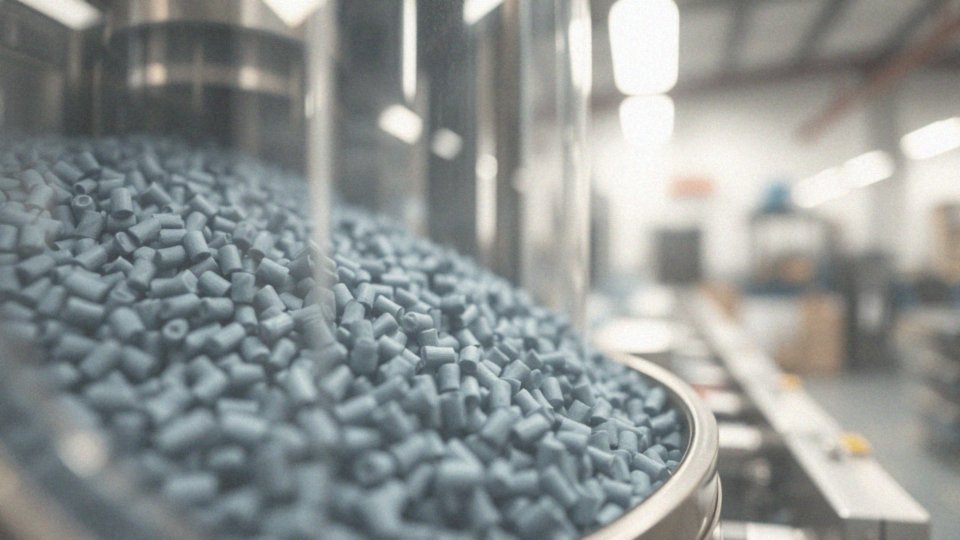
Temperatura odgrywa kluczową rolę w procesie topienia plastiku, bezpośrednio wpływając na jego właściwości, takie jak lepkość i płynność. Precyzyjna kontrola tego parametru jest niezbędna do uzyskania wysokiej jakości, jednolitego materiału. Odpowiednia temperatura minimalizuje ryzyko degradacji polimeru. Zbyt wysokie ciepło może prowadzić do niepożądanych skutków, w tym spalenia, zwęglenia, a nawet rozpadu cząsteczek tworzywa, co z kolei może skutkować wydzielaniem szkodliwych substancji, włączając w to dioksyny. Z drugiej strony, zbyt niska temperatura uniemożliwi efektywne przetworzenie materiału. Dostosowanie temperatury do konkretnego rodzaju plastiku gwarantuje optymalne parametry całego procesu. Ma to szczególne znaczenie w technikach takich jak formowanie wtryskowe, wytłaczanie i termoformowanie, gdzie precyzja jest kluczowa.
Jak przebiega proces przetapiania plastiku?
Przetwarzanie plastiku to złożony proces, który przekształca odpady z tworzyw sztucznych w cenne surowce wtórne, gotowe do ponownego wykorzystania. Pierwszym, niezwykle istotnym etapem jest segregacja, która pozwala na wyodrębnienie poszczególnych rodzajów plastików. Następnie, wyselekcjonowane tworzywa poddawane są rozdrabnianiu, gdzie specjalistyczne maszyny tną je na drobne fragmenty. Zwiększenie powierzchni materiału w ten sposób znacząco ułatwia dalszą obróbkę. Rozdrobniony surowiec trafia następnie do reaktorów lub wytłaczarek, gdzie pod wpływem precyzyjnie kontrolowanej temperatury ulega stopieniu. Kontrola temperatury jest kluczowa, ponieważ różne rodzaje plastików wymagają różnych zakresów temperatur. Zbyt wysoka temperatura może doprowadzić do degradacji polimeru i uwolnienia szkodliwych substancji, natomiast zbyt niska uniemożliwi skuteczne stopienie. Stopiony plastik jest następnie formowany w nowe produkty lub przetwarzany na granulki – uniwersalny surowiec do produkcji różnorodnych wyrobów z tworzyw sztucznych. Cały ten proces stanowi doskonały przykład gospodarki o obiegu zamkniętym.
Odpowiednia segregacja plastiku jest absolutnie fundamentalna dla efektywnego procesu topienia. Różne typy plastików charakteryzują się odmiennymi właściwościami, a ich mieszanie może obniżyć jakość uzyskanego materiału, skutkując wadliwymi produktami lub nawet uszkodzeniami maszyn. Staranna segregacja minimalizuje potencjalne problemy związane z materiałem, zapewniając optymalne parametry procesu. Ponadto, ułatwia dopasowanie parametrów procesu, takich jak temperatura, ciśnienie i czas, do konkretnego rodzaju tworzywa, co przekłada się na wyższą jakość produktu i zmniejszone zużycie energii. Recykling plastiku staje się znacznie efektywniejszy, gdy surowiec jest jednorodny, a dokładna segregacja podnosi jego wartość, czyniąc recykling bardziej opłacalnym.
W procesie recyklingu plastiku wykorzystuje się różnorodne maszyny, dostosowane do poszczególnych etapów. Do rozdrabniania używane są rozdrabniarki (młyny), które zmniejszają duże elementy na mniejsze fragmenty, oraz granulatory, przetwarzające odpady na granulat. Do przetapiania stosuje się wytłaczarki, które topią plastik i przepychają go przez dyszę, tworząc rury, folie lub płyty, wtryskarki, formujące skomplikowane kształty poprzez wtryskiwanie stopionego plastiku do form, oraz piece do topienia, przeznaczone do przetapiania dużych ilości plastiku w kontrolowanych warunkach. Dodatkowo, linie do mycia i suszenia przygotowują odpady do dalszej obróbki. Wybór odpowiedniej maszyny zależy od rodzaju przetwarzanego plastiku oraz pożądanego produktu końcowego.
Należy pamiętać, że wysokotemperaturowe przetapianie plastiku wiąże się z potencjalnymi zagrożeniami. Emisja szkodliwych substancji, takich jak dioksyny, furany i pyły, powstających podczas spalania, stanowi poważny problem. Istnieje również ryzyko samozapłonu, wynikające z gromadzenia się gazów mogących prowadzić do wybuchu. Brak odpowiedniej wentylacji i kontroli temperatury znacząco zwiększa te zagrożenia. Przetwarzanie PVC może powodować uwalnianie chlorowodoru (HCl), drażniącego gazu, dlatego kluczowe jest oczyszczanie spalin i przestrzeganie rygorystycznych zasad bezpieczeństwa.
Alternatywą dla spalania i składowania jest piroliza plastiku – proces rozkładu polimerów zachodzący bez dostępu powietrza. W tym procesie plastik podgrzewany jest do wysokiej temperatury (zwykle od 300°C do 900°C, w zależności od rodzaju plastiku), co prowadzi do jego rozkładu na gazy, ciecze (olej pirolityczny) i węgiel. Piroliza przekształca odpady w surowce, które mogą być wykorzystane jako paliwo lub do produkcji innych materiałów, przyczyniając się do zmniejszenia zanieczyszczenia środowiska.
Jak segregacja tworzyw sztucznych wpływa na proces ich topnienia?
Segregacja plastików to fundament efektywnego recyklingu, ponieważ różne tworzywa sztuczne charakteryzują się odmiennymi temperaturami topnienia. Niewłaściwe połączenie różnych typów plastiku, jak na przykład polietylenu (PE) z polichlorkiem winylu (PVC), może poważnie zakłócić proces obróbki. W takim przypadku PVC ulegnie zniszczeniu zanim PE zdąży się stopić.
Zatem, precyzyjna segregacja, gwarantując przetwarzanie jednorodnych materiałów, bezpośrednio wpływa na jakość produktu finalnego i ogranicza ryzyko powstawania szkodliwych emisji. Dzięki niej możliwe jest optymalne dopasowanie temperatury i czasu topnienia, co z kolei przekłada się na wyższą wydajność całego procesu recyklingu i znaczącą poprawę jakości uzyskiwanego tworzywa.
Jakie maszyny są używane do przetapiania i rozdrabniania plastiku?
Do rozdrabniania tworzyw sztucznych służą specjalistyczne urządzenia, powszechnie znane jako rozdrabniarki lub młyny, których zadaniem jest zmniejszenie objętości plastikowych odpadów, przygotowując je tym samym do dalszych procesów recyklingowych. Przetapianie plastiku odbywa się z wykorzystaniem zróżnicowanego sprzętu.
Do tego celu wykorzystuje się:
- wytłaczarki, pozwalające na formowanie tworzywa w nowe kształty,
- piece, zapewniające jego stopienie,
- wtryskarki, umożliwiające tworzenie precyzyjnych detali,
- urządzenia do pirolizy, czyli termicznego rozkładu plastiku.
Ciekawą alternatywę proponuje projekt „Precious Plastic„, który umożliwia budowę modułowych maszyn. Dzięki niemu można we własnym zakresie zbudować rozdrabniarkę, wtryskarkę lub wytłaczarkę, korzystając z dostępnych instrukcji, które szczegółowo prowadzą przez cały proces. To rozwiązanie znacznie zwiększa dostępność recyklingu plastiku.
Jakie są zagrożenia związane z wysokotemperaturowym przetapianiem plastiku?
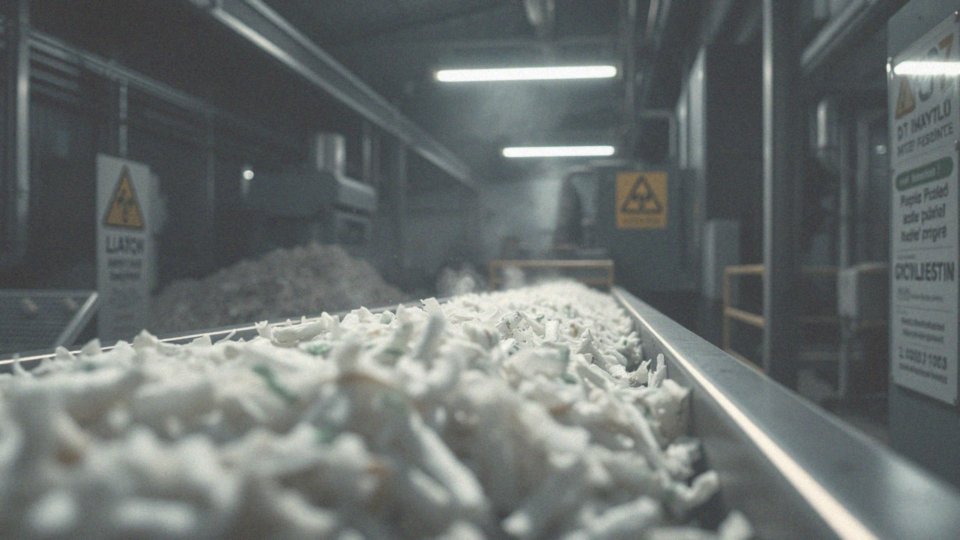
Wysokotemperaturowe przetapianie plastiku to operacja obarczona realnym niebezpieczeństwem. Podczas tego procesu generowane są toksyczne związki, w tym wyjątkowo groźne dla zdrowia dioksyny i furany. Przekroczenie dopuszczalnej temperatury skutkuje degradacją termiczną tworzywa, co z kolei prowadzi do uwalniania lotnych związków organicznych. Dodatkowo, zmieniają się jego parametry wytrzymałościowe. Nieprawidłowo przeprowadzony proces stwarza podwyższone ryzyko pożaru, a nawet eksplozji. Przetwarzanie PVC wiąże się z powstawaniem chlorowodoru (HCl), niebezpiecznego produktu rozkładu. Gaz ten nie tylko powoduje korozję urządzeń, ale również negatywnie wpływa na nasze zdrowie. Z tego względu kluczowe jest przestrzeganie zasad bezpieczeństwa, w tym stały monitoring emisji i sprawne systemy wentylacyjne, które stanowią podstawowy element bezpiecznej pracy.
Co to jest piroliza plastiku i w jakiej temperaturze zachodzi?
Piroliza to kluczowy proces rozkładu termicznego tworzyw sztucznych w warunkach beztlenowych. Przekształca ona odpady plastikowe w cenne surowce, takie jak:
- gaz,
- olej pirolityczny,
- węgiel.
Te produkty mogą być wykorzystywane jako paliwa i substraty w różnorodnych procesach przemysłu chemicznego. Optymalna temperatura pirolizy, zazwyczaj mieszcząca się w przedziale od 300°C do 900°C, jest ściśle uzależniona od rodzaju przetwarzanego polimeru. Inne warunki sprzyjają efektywnemu rozkładowi polietylenu, a inne polipropylenu. Stanowiąc formę recyklingu chemicznego, piroliza pozwala na odzyskiwanie wartościowych substancji z plastikowych odpadów, jednocześnie przyczyniając się do redukcji objętości składowanych śmieci, co przynosi istotne korzyści dla środowiska.